Portfolio
Our services include above all the high-precision area of CNC production and assembly. The combination of different manufacturing techniques, paired with years of experience and expertise of our competent and regularly trained specialists, set us apart.
Our machines in the fully air-conditioned production are centrally extracted and are connected to a central cooling water system. Measurement protocols and clean room assembly help to meet our high quality standards. Thanks to the new facilities, all of our regularly audited production processes in the well thought-out machine park will be optimized again. Information about properties and equipment can be found in the machine list.
In order to be able to meet all our standards, we use versatile materials such as steel, aluminum, non-ferrous and hard metals, plastics, ceramics and glass.
CNC milling techniques
We mill complex individual parts as well as small series in 3, 4 and 5 axes up to sizes of 3400 x 3400 x 2000 mm (X x Y x Z).
Some of our 5-axis machines are equipped with rotary tables and can therefore also be used as a combined milling and turning machine in order to be able to carry out several work steps in one setting.
A robot-automated production cell serves three Hermle C42s and ensures efficient, flexible and intelligent use of the machines.
In 2020 a DMG 340 µ-precision will be put into operation, with which we can process large parts with the µ-precision optimizations from DMG. The new DMG 210 µ-precision achieves a positioning accuracy of 4 µ on the linear axes. For this purpose, precisely dimensioned, reinforced foundations were installed in the floors.








CNC turning techniques
When it comes to turning, our focus is on the production of complex small series, which we can realize with our various lathes.
Our DMG CTX TC beta and gamma have both a turret with driven tools and a separate milling spindle for combined processing. Almost all of our lathes have a counter spindle so that components can be machined on 6 sides.
Long turning is also part of our repertoire, which we can do with our Traub TNL up to a diameter of 32 mm. The machines are equipped with an additional turret with an integrated B swivel axis, which also contains driven tools.
Electrical Discharge Machining
We offer both wire (600x400x450mm) and die sink EDM (900x750x450mm) in-house. For wire EDM, we also have a controlled positioning axis (e.g. for helices) and a rotation axis (rotary eroding).


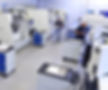



Ultrasonic / HSC processing
With the help of ultrasonic, we can also machine hard and very brittle materials (glass, ceramics, hard metals) in five axes.
In addition to ultrasonic machining for brittle materials, our two Sauer Ultrasonic machines also enable high-speed cutting (HSC) to mill the finest components at increased speeds.
Further procedures
Of course, various grinding techniques are also part of our production spectrum, including:
-
Flat grinding
-
Round table grinding
-
Cylindrical grinding
We also offer the following manufacturing processes in-house:
-
Lapping and honing
-
Embossing and punching
-
Saws
-
Water jet cutting
-
Slide grinding
-
Laser marking and laser engraving
-
Passivation and electropolishing
-
Glow and aging
-
Sandblasting, glass bead blasting and aerolap polishing
-
paint
-
Welding and laser welding
-
soldering
For other hardening processes such as nitriding, colsterizing, vacuum hardening or hard coating, as well as galvanic finishing techniques such as anodizing, we work closely with proven partners.







Project management
Our engineers and project managers accompany the manufacturing process of complex components and assemblies. We stand by our customer's side right from the beginning and advise on manufacturability, material, manufacturing options and optimal, cost-efficient processes.
Furthermore, we will accompany and supervise the projects in every production stage in-house and with our proven partners in close cooperation with our customers. The entire supply chain management of the external services is also organized by our project managers.
We always look for solutions together with our customers when handling individual and complex projects. We benefit from our longstanding experience in order to be able to achieve first-class and high-precision results in challenging projects.
We attach particular importance to quality assurance - constant checking and measuring between the production steps, cleanliness and test execution (e.g. leak test, shock test test) are regularly initiated and carried out under the personal supervision of the project representative, especially after external production steps.
Metrology
State-of-the-art tactile and optical metrology devices in an air-conditioned, clean room-filtered environment are being used by our quality assurance team. The measuring rooms are equipped with vibration dampers at the transitions to the halls in order to carry out measurements with µ-accuracy. Some of our measuring room foundations are completely decoupled from the rest of the building and anchored meters deep.
Zeiss coordinate measuring machines (CMMs) such as our Zeiss PRISMOs (active scanning sensor with high-resolution inductive system VAST Gold and built-in rotary table) guarantee maximum precision in the manufacturing process through tactile, scanning, or optical measurements.
A Zeiss O-INSPECT (combined tactile and optical measurement), which is ideal for measuring small components, and a Zeiss MMZ for large parts (6000 x 3000 x 2000mm) complete our portfolio of ten high-quality Zeiss metrology machines.
Specially trained employees ensure that our products always meet our customers' requirements.
We have had our high quality standards confirmed and certified by an external service provider in a measurement process assessment.



Assembly and clean room assembly
In general, we offer the assembly of entire assemblies or devices in parts or to complete devices with corresponding tests.
Our clean rooms correspond to ISO class 6.
In these, cleaning as well as assembly and packaging can be carried out professionally according to the requirements.
Optionally, the assembly can also be carried out in a clean room.
In order to clean the workpieces, we have three Miele fully automatic industrial cleaning machines with water desalination and a locked pass-through function into the clean room, as well as three ultrasonic cleaning baths.
Thanks to our equipment and our trained and qualified staff, it is possible for us to guarantee the highest standards by keeping the environment under controlled and constant conditions clean.
Our production range at a glance
CNC milling: 5-axis simultaneous up to 3,400 x 3,400 x 2,000 mm
CNC turning: up to a length of 2,000 mm
CNC long turning: up to Ø32 mm
Combined CNC milling and turning: 5-axis up to a diameter of 2,200 x 1,300 mm
CNC wire EDM: x / y / z-axis up to 600 x 400 x 400 mm with positioning axis or rotation axis
CNC die sinking: x / y / z axis up to 900 x 750 x 450 mm
Ultrasonic / HSC machining: 5-axis, with ultrasound
CNC water jet cutting: up to 1,550 x 3,050 mm, 3 or 5 axes
Flat grinding up to 2,000 x 1,000 mm and rotary table grinding up to Ø600 mm
Clean room: clean room assembly, clean room packaging



